BB 25660
Travaux de remise en état du moteur de traction 2
(février à octobre 2017)
|
|
Suite à l’arrivée de la BB 25660 le 29 Novembre 2016, une série de vérifications portant sur les organes vitaux de la machine est effectuée afin d’avoir une vision sur l’état de ces derniers dans le but d’assurer une préservation sereine.
Le premier de ces contrôles a lieu le 4 février 2017 et concerne les deux moteurs de traction. En effet, les moteurs de traction sont les pièces maîtresses d’une locomotive. Sans eux, il est impossible de rouler. De par leur emplacement dans la locomotive et leur masse, il n’est pas envisageable de remplacer un moteur de traction sans disposer d'un matériel spécifique nécessaire à des opérations de levage coûteuses. Il faut donc que ces derniers soient en bon état général.
Les moteurs de traction utilisés depuis les débuts de la traction électrique jusqu’aux BB de 4 400 kW (dernières séries à en être équipées) sont des moteurs à courant continu. Tout comme la CC 6570, la BB 25660 est équipée de deux moteurs de traction à courant continu à excitation en série.
Les moteurs à courant continu sont des machines robustes mais demandent un soin particulier sans quoi des défauts plus ou moins sérieux peuvent survenir sur ces derniers lors de leur utilisation et même lors de périodes d’inactivité.
La BB 25660 est équipée de deux moteurs de traction TAB 660 dont voici quelques caractéristiques :
- Tension d’alimentation : 1 500 V continu
- Intensité absorbée : 1 050 A
- Puissance utile : 1 470 kW (soit 2 000 ch)
- Vitesse de rotation : 1 430 tr/min
- Masse : 5 330 Kg
- Ventilation nécessaire (débit d’air) : 180 m3/min
Constitution d’un moteur de traction à courant continu :
Un moteur à courant continu se compose de deux parties essentielles :
- l’inducteur (carcasse fixe du moteur appelée aussi « stator ») ;
- l’induit (partie tournante du moteur appelé également « rotor »).
Induit et inducteur sont bobinés, c’est-à-dire que ces pièces portent des bobines de fil qui vont, une fois parcourues par un courant électrique, générer des champs magnétiques visant à faire tourner l’induit. Ce dernier entraîne les essieux de la locomotive via un réducteur à engrenages.
Constitution de l’inducteur :
L’inducteur est la partie fixe du moteur (stator). L’inducteur se compose de différents pôles :
- Six pôles principaux ;
- Six pôles auxiliaires (ou pôles de commutation) ;
- Six pôles de compensation (montés sur le même noyau que les pôles principaux).
Les pôles principaux génèrent le champ magnétique nécessaire au fonctionnement du moteur.
Les pôles auxiliaires (ou pôles de commutation) sont placés entre les pôles principaux. Ils permettent de limiter la formation d’arcs électriques entre le collecteur et les balais.
Les pôles de compensation permettent de lutter contre la distorsion du flux magnétique dans l’entrefer (espace entre le stator et le rotor) du moteur (phénomène existant sur les moteurs de forte puissance ayant pour conséquence de décaler la ligne neutre du moteur et générer des problèmes de commutation).
Constitution de l’induit :
L’induit est la partie en rotation du moteur (rotor). L’induit se compose :
- D’un arbre ;
- D’un circuit magnétique ;
- D’un collecteur ;
- D’un bobinage.
L’arbre est maintenu par deux roulements montés sur les flasques du moteur. Sur une extrémité de cet arbre on vient monter un accouplement Citroën assurant la liaison mécanique entre moteur et réducteur.
Le circuit magnétique, constitué de tôles, est monté sur l’arbre. Celui-ci est encoché sur toute sa longueur.
Le bobinage est constitué par des conducteurs de cuivre qui prennent place dans les encoches du circuit magnétique. Les extrémités du bobinage sont raccordées au collecteur.
Le collecteur est constitué d’un ensemble de lames de cuivre, les entrées/sorties des bobines de l’induit y sont raccordées par brasure.
Eléments annexes :
- Les balais ;
- Les porte-balais.
L’alimentation de l’induit est réalisée par un contact glissant au moyen de balais en carbone venant frotter sur le collecteur. Les balais sont maintenus en appui sur le collecteur par des portes-balais équipés de ressorts. A mesure que les balais s’usent par frottement, les ressorts compensent pour maintenir une pression mécanique constante.
Il y a six porte-balais dans un moteur de traction TAB 660 et chaque porte-balais possède quatre balais. Il y a donc au total vingt-quatre balais en carbone répartis sur le pourtour du collecteur.
Etant donné que l’accès au collecteur s’effectue par une seule trappe de visite, les portes-balais sont montés sur une couronne métallique (couronne porte-balais). Cette couronne peut être mise en rotation à la main afin d’amener les portes-balais en regard avec la trappe de visite dans le but de procéder au remplacement des balais par exemple.
Isolation des bobinages
Les bobinages constituant le moteur sont réalisés avec des fils de forte section en cuivre. Ces fils sont isolés au moyen de rubans isolants.
Pour finir, le moteur est dit « à excitation en série » car l’induit et l’inducteur sont connectés en série. La valeur du courant d’excitation parcourant l’inducteur est la même que celle parcourant l’induit. Un moteur à excitation série développe un couple qui est fonction du courant traversant le moteur. Plus l’intensité du courant est élevée, plus le couple est élevé. Ce type de moteur est donc bien adapté à la traction électrique de par son fort couple au démarrage.
Chronologie des travaux :
Mesures effectuées :
Un des paramètres les plus importants sur un moteur de traction est l’isolement. En effet, les bobines sont isolées les unes par rapport aux autres et par rapport à la masse au moyen de rubans isolant entourant les conducteurs électriques. Si l’isolation ne joue plus son rôle, des courts-circuits entre les bobines et ou entre les bobines et la masse sont à craindre. Avec des tensions de l’ordre de 1 500 Volts, un court-circuit se traduit par un violent amorçage pouvant littéralement brûler l’intérieur du moteur nécessitant sa dépose et la réfection totale des bobinages endommagés.
Afin de juger de l’état des isolations, une mesure appelée « mesure d’isolement » réalisée à l’aide d’un appareil nommé « mégohmmètre » permet de savoir rapidement si les isolations sont en bon état ou non.
Le 4 Février 2017, après lecture des schémas électriques de la BB 25660, nous définissons les points du circuit sur lesquels nous pouvons raccorder le mégohmmètre afin de mesurer l’isolement de l’induit et de l’inducteur de chaque moteur de traction.
Le principe de la mesure est le suivant : l’appareil est muni de deux fils, l’un est branché à la masse de la machine (caisse par exemple) l’autre est branché sur les bornes du bobinage à mesurer. Après mise en marche de l’appareil, ce dernier injecte une tension de test de 2 500 Volts entre masse et bobinage. Les fuites de courant à travers les isolations sont mesurées et le mégohmmètre calcule leur valeur en ohms. La limite en dessous de laquelle le moteur n’est pas utilisable est de 3 mégohms (soit 3 millions d’ohms). A noter que les valeurs d’isolement varient beaucoup en fonction de la météo (l’humidité à tendance à imprégner les isolations du moteur rendant les valeurs d’isolement basses). Dans ce dernier cas, un réchauffage du moteur au moyen d’un générateur à air chaud permet de faire remonter les valeurs d’isolement dans la norme.
Lors de la mesure d’isolement du moteur de traction n°1, nous avons relevé les valeurs suivantes :
- Inducteur : 15,6 MΩ
- Induit : 575 MΩ
La limite étant à 3 mégohms, nous sommes largement au-dessus donc l’isolement de ce moteur est tout à fait conforme.
Concernant le moteur de traction n°2, les valeurs ne furent pas enthousiasmantes :
- Inducteur : 750 MΩ
- Induit : 0,27 MΩ
Nous pouvons nous rendre compte que l’induit présente un sérieux défaut d’isolement.
Même après la mise en place d’un réchauffeur afin de faire disparaître les traces d’humidité, les valeurs d’isolement de l’induit ne remontent absolument pas. Pour autant, il n’est pas exclu que le défaut d’isolement ne se situe pas dans une partie accessible du moteur (boîte à bornes, câblage, etc…) donc éventuellement réparable. En effet, lorsque nous mesurons l’isolement de l’induit, nous mesurons en fait le « circuit induit »comprenant : les câbles d’alimentation du moteur, la boîte à bornes, les isolateurs de portes-balais, les connexions de la couronne porte-balais, les pôles auxiliaires, les pôles de compensation et l’induit. Le défaut d’isolement peut se situer sur l’un de ces éléments dont certains peuvent être réparés directement dans la machine sans procéder à un levage et une dépose du moteur.
Quelques opérations vont être nécessaires afin de séparer électriquement les éléments cités plus haut dans le but de définir quel est l’élément qui est en défaut.
Etape n°1 (19 février 2017) :
Permettre la mise "au point mort" des réducteurs afin de rendre libre la rotation de l’induit.
Les BB 25500 étant équipées de bogies monomoteurs à deux rapports d’engrenage (marchandises/voyageurs), une troisième position du réducteur permet de désolidariser mécaniquement le moteur des essieux : c’est la position « point mort ». Pour ce faire, le mécanisme de déverrouillage est manœuvré, le réducteur est placé entre les positions marchandise et voyageur, et l’ensemble est reverouillé.
Cependant, ce dispositif n’étant plus utilisé régulièrement ces dernières années, le système de verrouillage s'avère grippé sur la 25660. Impossible de le faire bouger à la main. Quelques heures de travail plus tard et avec l’aide du dégrippant, les mécanismes sont de nouveau opérationnels et le réducteur est placé au point mort. Nous pouvons ainsi faire tourner l’induit à la main et observer visuellement son état au fur et à mesure de sa rotation. Visiblement, l’induit et son collecteur présentent un aspect propre, sans traces d’amorçages visible.
|
|
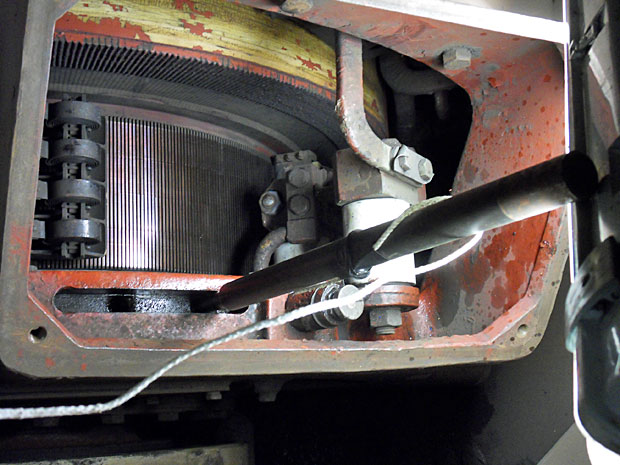 |
Etape n°2 (4 mars 2017) :
Procéder à la rotation de la couronne porte-balais.
Les portes-balais, au nombre de six, sont montés sur une couronne métallique appelée « couronne porte-balais ». Là encore, le dispositif de verrouillage de la couronne porte-balais est grippé et il nous faudra patience, force et dégrippant afin de la débloquer.
Ci-contre : la barre à virer est insérée dans la couronne porte-balais afin de la faire tourner manuellement. |
|
A mesure que nous faisons tourner manuellement la couronne porte-balais sur le moteur 2 de la BB 25660, les dégâts apparaissent à nos yeux. Les isolateurs sont noircis et les barres de connexion sont complètement brûlées. Pas de doute, l’amorçage à bien eu lieu sur la couronne porte-balais.
Ci-dessous : vue sur les barres de la couronne porte-balais : les isolations sont complètement carbonisées. |
|
|
Il faut savoir maintenant si d’autres éléments sont touchés par un défaut d’isolement avant d’envisager une réparation ou non. En effet, le circuit induit comprend plusieurs éléments (dont la couronne porte-balais) qui vont être déconnectés les uns par rapport aux autres et testés un par un.
Voici les éléments constituants le circuit induit qui sont déconnectés afin de réaliser les mesures :
- Les câbles d’alimentation du moteur (séparation du moteur par rapport à l’armoire d’appareillage attenante) ;
- La couronne porte-balais est décalée (séparation entre boite à borne du moteur et couronne porte-balais) ;
- Tout les balais sont retirés (séparation entre couronne porte balais et induit).
Tous ces éléments furent testés un par un et en voici les résultats :
- Isolement câblage, boîte à borne et alimentation de la couronne porte balais « + » : 244 MΩ
- Isolement pôles auxiliaires et pôles de compensation : 183 MΩ
- Isolement induit : 4,04 GΩ
- Isolement couronne porte-balais « + » : 0,27 MΩ
- Isolement couronne porte-balais « - » : 9,95 GΩ
Au vu des résultats, il apparait clairement que le défaut d’isolement se situe sur une des deux couronnes porte-balais. L’induit a un isolement excellent ainsi que le reste des bobinages du moteur.
Après observation, il serait apparemment possible de déposer les deux barres de cuivre constituant la couronne porte-balais et de refaire leurs isolations. Le démontage de ces barres implique un accès sur le flasque du moteur, deux trappes sont présentes sous le plancher. |
|
|
Etape n°3 (11 mars 2017) :
Dépose du plancher au-dessus du bogie afin d’accéder au deux petites trappes disposées sur le flasque du moteur.
Le plancher en aluminium est maintenu par une multitude de vis qui, par le temps ont bien évidement rouillé rendant leur démontage impossible. Marteau, burin et une après-midi de travail seront de rigueur afin de les retirer et permettre ainsi la dépose du plancher.
Ci-contre à gauche et ci-dessous : dépose du plancher en aluminium (vue sur le réducteur et l’accouplement Citroën) et dépose des petites trappes sur le flasque (vue sur une barre brûlée)
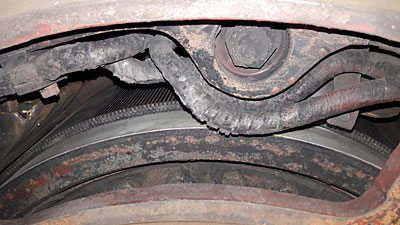
|
|
Etape n° 4 (14 mars 2017) :
Commande des matériaux d’isolation.
Après une prise de renseignement auprès d’un contact des ateliers d’Hellemmes (atelier spécialisé dans la réfection des transformateurs et moteurs de traction), nous commandons les différents types de rubans isolants.
Ci-contre : les différents types de rubans isolants. De gauche à droite : le kapton, l’isomica, l’epoflex et l’élasto-silicone auto-amalgamant. |
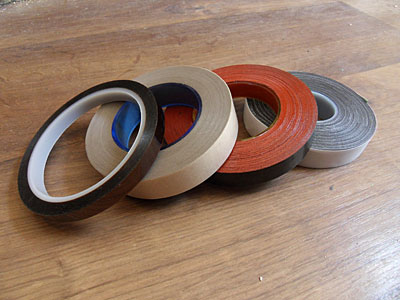 |
|
Etape n°5 (08 avril 2017) :
Démontage des connexions de la couronne porte-balais et dépose des portes-balais.
Afin de déposer les deux barres circulaires formant la couronne porte-balais il convient de la déconnecter des portes-balais eux-mêmes. Six cosses assurent la connexion électrique. Après déconnexion, les six portes-balais entiers sont déposés (isolateur + porte-balais).
Ci-dessous : à gauche, les six portes-balais et leurs isolateurs sont déposés. A droite, vue sur les cosses des barres à déposer. |
|
|
Etant donné que les barres de cuivre vont être posées sur le collecteur dans le but de les ré-isoler, il convient de protéger ce dernier afin de ne pas rayer ou abîmer les lames de cuivre le constituant. Pour ce faire, nous posons l’extrémité d’un film plastique sur le collecteur et faisons tourner l’induit à la main afin d’enrouler le film plastique autour du collecteur. Un rouleau entier (soit 50 mètres) sera nécessaire afin d’assurer une protection efficace.
Ci-dessous : la protection du collecteur. |
|
|
S’en suit la dépose proprement dite des barres. Les deux barres de cuivre sont maintenues fixées à la carcasse au moyen de dix brides en laiton. Elles sont déposées au fur et à mesure libérant ainsi les deux barres qui sont ensuite posées sur le collecteur préalablement protégé.
Ci-dessous : dépose des brides et mise en place des barres sur le collecteur protégé. |
|
|
Etape n°6 (29 avril et 27 mai 2017) :
Retrait des isolations.
Les deux barres étant posées sur le collecteur, il convient maintenant de retirer la totalité des isolations. Dans un premier temps, les isolations sont découpées au moyen d’un cutter puis, dans un deuxième temps, les barres sont brossées à l’aide d’une brosse rotative en nylon montée sur une polisseuse pneumatique. Cette opération permet de retirer la colle et les dernières particules de rubans isolants qui n’ont pu être retirés au cutter. Ceci permet également de rendre les barres de cuivre parfaitement polies et exemptes d’aspérités. Cette opération, de par la difficulté d’accès, a été particulièrement pénible et fastidieuse.
Ci-dessous : le retrait des isolations, puis le polissage des barres. |
|
|
|
Etape n°7 (24 juin, 1er, 22 et 29 juillet 2017) :
Isolation des barres et remise en état des supports isolateurs de portes-balais.
Les isolateurs de portes-balais étant en mauvais état, ces derniers sont brossés et repeints au vernis anti-flash. Ce dernier est un vernis possédant un haut pouvoir isolant, il est appliqué simplement au pinceau en deux couches.
Concernant la réfection des isolations, les deux barres de cuivre constituant la couronne porte-balais sont en réalité constituées de deux sections chacune. Il y a donc quatre sections à ré-isoler. A raison d’une section par journée, ce sont quatre journées qui seront nécessaire pour mener à bien ce travail.
L’isolation est réalisée au moyen de rubans isolants ayant chacun des propriétés particulières. Une première couche de ruban adhésif polyamide « kapton » est appliqué sur la barre de cuivre constituant ainsi une isolation primaire.
Ci-dessous : pose du ruban adhésif polyamide « kapton ». |
|
|
Puis, deux couches de ruban minéral « isomica » sont posées. Ce ruban contient du mica (roche feuilletée ayant des propriétés isolantes et possédant une grande tenue aux fortes températures). Il constitue l’isolation secondaire.
Ci-dessous : pose du ruban minéral « isomica ». |
|
|
On termine par une couche de ruban polyesters « epoflex ». Ce ruban assure la protection mécanique des isolations précédentes. Il protège également les autres isolations de l’humidité et des pollutions (poussière de balais, etc…). A noter que le ruban « isomica » n’est pas autocollant, il faut donc le poser et le coller par polymérisation à l’aide d’un décapeur thermique.
Ci-dessous : pose du ruban polyesters « epoflex ». |
|
|
Les barres ayant une forme circulaire, il nous était impossible de les sortir de l’intérieur du moteur. C’est donc par la trappe de visite que ces dernières ont été ré-isolées. A mesure que le travail d’isolation progresse, les barres sont protégées avec de la mousse et du ruban adhésif afin de ne pas blesser les isolations toutes neuves lors de la manipulation des barres dans le moteur.
Ci-dessous : protection provisoire des barres isolées (mousse + ruban adhésif). |
|
|
|
Etape n°8 (19 août 2017) :
Remontage des isolateurs et des barres.
Les deux barres ré-isolées sont positionnées à leur emplacement respectif. On monte un premier isolateur de porte-balais et on connecte sans serrer la cosse de la barre à ce dernier (photo ci-contre).
On tourne la couronne porte-balais jusqu’au prochain emplacement d’isolateur, on monte ce dernier et on connecte la cosse comme précédemment. On procède ainsi pour les six isolateurs de portes - balais. Nous positionnons ensuite les brides en laiton (préalablement peintes à l’anti-flash) afin de fixer les barres à la carcasse sans les serrer.
Ci-dessous : les brides polies et peintes à l’anti-flash. |
|
|
Au fur et à mesure que les brides sont posées, nous mesurons l’isolement des barres par rapport à la carcasse afin d’écarter tout risque de mauvais montage (isolation endommagée lors du remontage par exemple).
Ci-dessous : mise en place des brides de maintien. |
|
|
Une fois que toutes les brides sont montées, on termine en serrant au couple les six isolateurs à la carcasse, les cosses assurant la connexion électrique et les dix brides de maintien des barres à la carcasse.
Aux extrémités des barres isolées, une couche de ruban élasto-siliconne auto-amalgamant est posée sur quelques centimètres afin d’arrêter les isolations évitant ainsi aux rubans isolants de se dérouler sous l’effet des vibrations ou de la ventilation forcée du moteur.
Ci-dessous : pose du ruban élasto-siliconne sur les extrémités des barres. |
|
|
A ce stade, une première couche de vernis anti-flash est appliquée sur l’induit, les barres et la carcasse environnante du moteur.
Ci-contre : application de la première couche de vernis anti-flash. |
|
|
Etape n°9 (16 septembre 2017) :
Remontage et réglage des portes-balais et des éclateurs.
Les six portes-balais sont fixés sur les isolateurs. Le réglage de leur hauteur par rapport au collecteur est réalisé. Les balais reprennent place dans les portes-balais et les éclateurs (assurant la sécurité du moteur contre les flashs liés au contact balais/collecteur) sont également montés et réglés.
Ci-dessous : porte-balais et balais. |
|
|
|
A ce stade, une mesure du faux rond du collecteur est réalisée au moyen d’un comparateur à cadran. Le collecteur présente un faux rond de 3 centièmes de millimètre, ce qui est conforme car la limite maximale est de 7 centièmes.
Ci-contre : mesure du faux rond du collecteur.
|
|
Etape n°10 (14 et 21 octobre 2017) :
Essais statiques et dynamiques du moteur.
Suite à la fin des travaux sur le moteur, il convient de valider son fonctionnement par une série de mesures et de tests d’ordre électriques.
Nous mesurons l’isolement des deux moteurs de traction en vue de réaliser les essais. Vu le temps humide qui régnait le 14 octobre, c’est sans grande surprise que les valeurs d’isolement ne sont pas conformes. Nous mettons donc en place sur chaque moteur un réchauffeur afin d’insuffler dans ces derniers un air chauffé à 60°C. L’air chaud va réchauffer progressivement les enroulements des moteurs afin d’éliminer les traces d’humidité absorbées par les isolants. Une semaine plus tard, soit le 21 octobre, de nouvelles mesures sont réalisées sur les deux moteurs. Un minimum de 3 mégohms (3 millions d’ohms) sous une tension de test de 2 500 V est requis sur l’isolement de l’induit et de l’inducteur afin de pouvoir tractionner sans crainte.
Voici les résultats :
Moteur 1 :
- Inducteur : 510 MΩ
- Induit : 69,5 MΩ
Moteur 2 :
- Inducteur : 20,8 MΩ
- Induit : 50 MΩ (nous somme bien loin des 0,27 MΩ d’avant les opérations de ré-isolation !)
Les valeurs étant toutes supérieures à 3 MΩ, les moteurs sont donc prêts à tractionner. Les essais se déroulent en deux temps : essais à poste fixe et essais en roulant.
A poste fixe, les essais consistent à faire tourner le moteur à vide afin de contrôler son fonctionnement à des vitesses de rotation proche de la vitesse nominale. Pour ce faire, les réducteurs sont placés en position « point mort », c’est-à-dire entre les positions « marchandise » et « voyageur ». Le moteur peut donc tourner librement sans entraîner les essieux.
Les deux pantos sont levés, le disjoncteur est fermé, un sens de marche est choisi et le cran 1 est enclenché pendant 2 secondes. Rapidement, le moteur démarre et prend de la vitesse.
Il convient d’être particulièrement vigilant lors de cette opération car les moteurs à courant continu à excitation en série partent à l’emballement lorsqu’ils tournent à vide (c’est-à-dire sans charge sur leur arbre). L’emballement du moteur conduit au défrettage de l’induit (les bobinages de l’induit sortent des encoches du rotor sous l’effet de la force centrifuge, il y a donc destruction totale du moteur).
L’opération de rotation à vide est effectuée dans les deux sens de marche, tout fonctionne correctement.
S’en suit l’essai de roulage dans le dépôt. La locomotive est déplacée dans les deux sens de marche sur quelques centaines de mètres, tout va bien, les essais sont terminés.
Ci-dessous : le moteur complètement remonté et prêt pour les essais. |
|
|
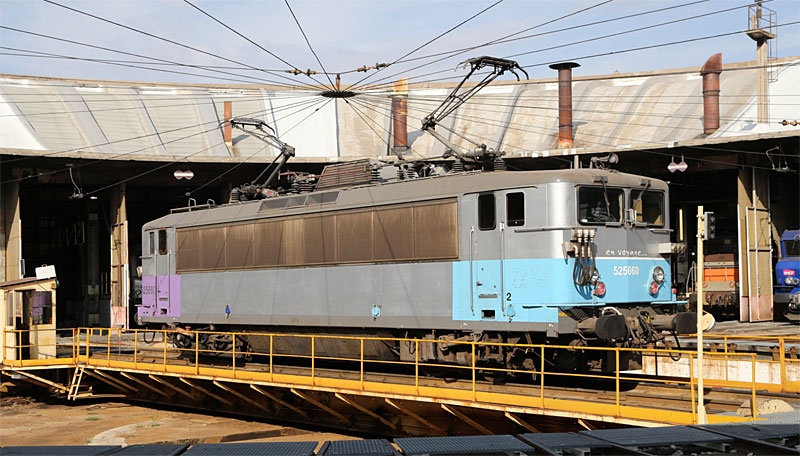
Ci-dessus : le 21 octobre 2017, la BB 25660 effectue son premier essai de traction, avec succès.
|
Conclusion :
En février 2017, alors que les premières mesures d’isolement déclaraient le moteur n°2 « mort », nous avons eu l’audace de relever le défi de tenter une réparation de ce dernier et c’est chose faite.
De par la complexité de l’opération et de sa mise en œuvre on notera qu’une telle opération n’a jamais vu le jour dans un dépôt mais plutôt dans un atelier directeur par démontage complet du moteur.
Le chantier fût particulièrement pénible mais en contrepartie, passionnant à réaliser et à organiser. Quelle belle récompense de voir la BB 25660 de nouveau opérationnelle !
Nous pouvons dire que l’audace a payé.
Texte et photos : Victorien Armand
(tous droits réservés)
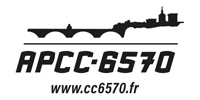
|
|
Reportage photo sur le premier essai de traction de la BB 25660 à l'issue des travaux sur le moteur 2 : cliquez ici
Reportage vidéo sur les évolutions de la BB 25660 lors de son premier essai de traction : cliquez ici
|
|
|
|
|